OEM and ODM Services for Medical Devices, Life Science Instruments, Robotics, and Healthcare IoT Innovations
ACHB Enterprise Co., LTD (ACHB) provides OEM and ODM services for medical devices, life science instruments, robotics and health related IoT devices. Our advancement in high precision manufacturing can be traced back across two decades of constant development, working hand in hand with our clients to create highly-effective solutions that provide a platform for continued growth and innovation every day.
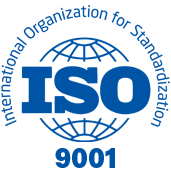
End-to-End Precision Manufacturing for Cost-Effective, High-Quality Production
Our ISO-certified facilities provide flexible solutions at every stage of the manufacturing process, from prototyping to full-scale production. With expertise in CNC machining, assemblies, plastic injection molding, and more, we deliver reliable, cost-efficient components that accelerate time-to-market and improve your bottom line.
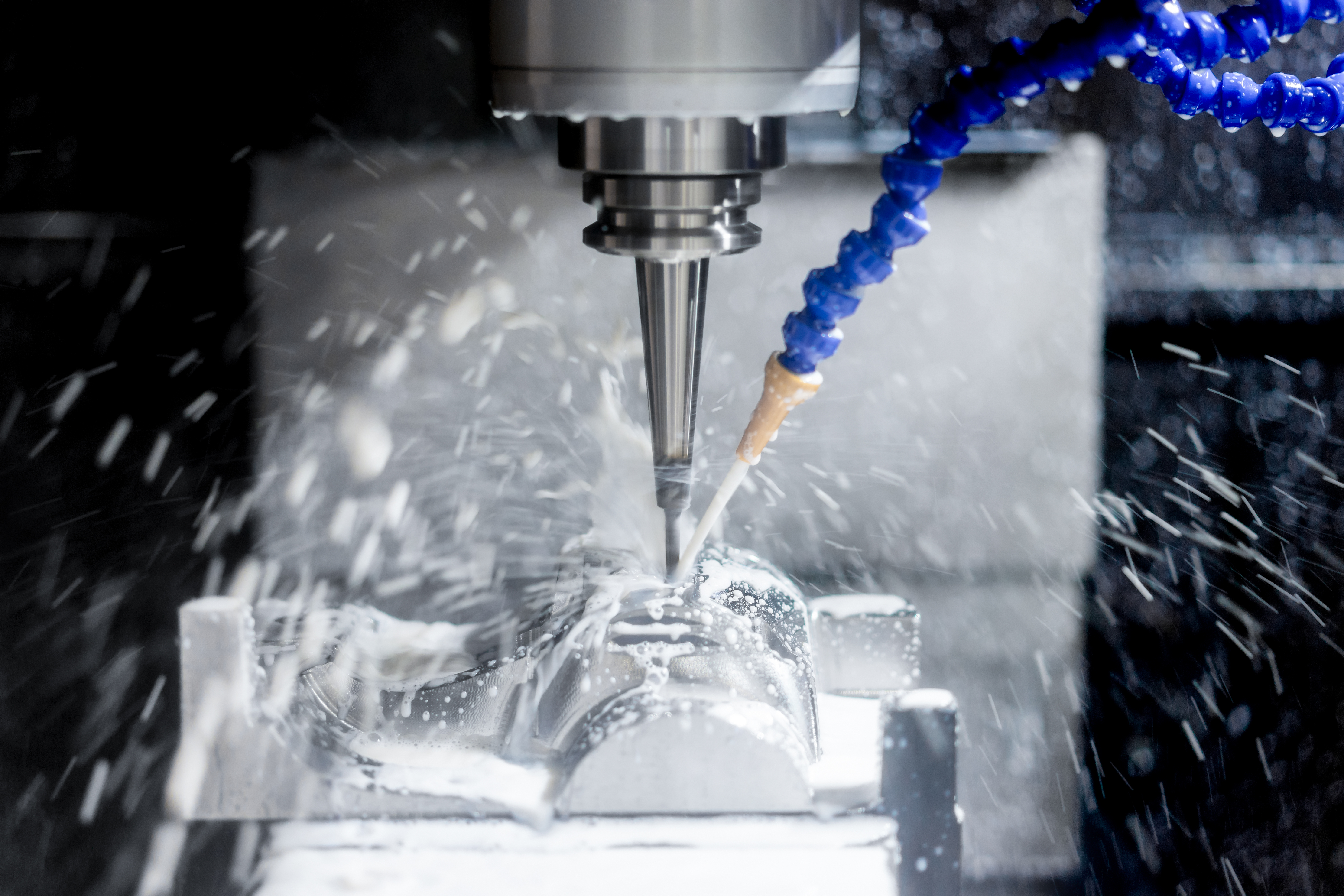
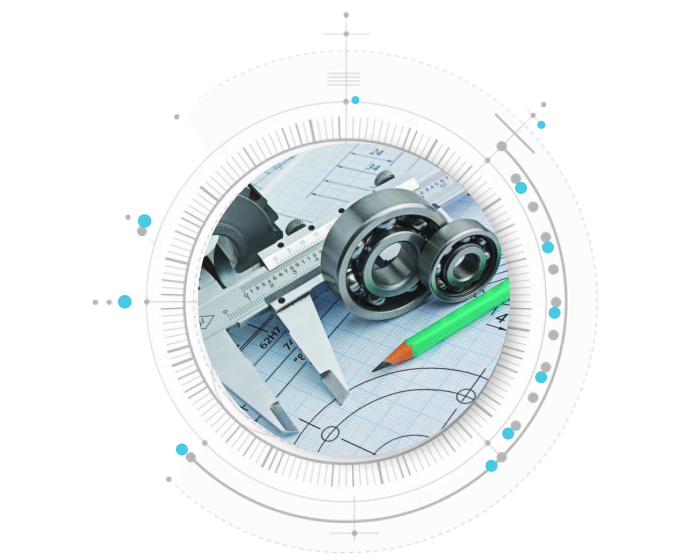
Medical Devices, Life Science Equipment, and Robotics Solutions
With decades of CNC machining experience and advanced material expertise, we support engineering teams in developing high-performance medical devices, life science equipment, and robotic systems. From concept prototyping to full-scale production, we optimize designs for reliability and ensure every project is executed with precision and dedication.
Industry Expertise
Our expert engineers help you stay competitive by delivering tailored solutions that meet your design needs. The ACHB team develops advanced medical devices, lab equipment, or robotics systems while meeting evolving customer demands. We provide OEMs with flexible, customized solutions that ensure precision, efficiency, and quality.
We bridge the gap between point-of-care (POC) device innovation and laboratory equipment manufacturing.
- Expertise Across Domains
- POC-Inspired Innovation
ACHB specializes in the design and manufacturing of Class I and II medical devices, incorporating advanced technologies like sensors, fluidics, optics, lasers, and ultrasound.
- Seamless Process
- Regulatory Know-How
Our expertise in robotics engineering helps clients push the boundaries of what’s possible in autonomous systems.
- Advanced Systems
- Rapid Prototyping
Success stories with industry leading customers
At ACHB, we don't just solve technical challenges—we partner with our clients to align our solutions with broader goals. By working closely with medical professionals and device manufacturers, we ensure that every system not only meets functional and regulatory requirements but also enhances the user experience, safety, and operational efficiency.
Delivering Excellence:
Precision, Efficiency, and Cost Savings That Drive Success
On-Time Delivery Rate
We achieve a 94% on-time delivery rate across all client projects, ensuring seamless operations for our partners.
Product Quality Metrics
Maintaining exceptional standards, our product defect rate is consistently below 98.7% over the past 3 years.
Cost Savings Achieved
Clients report an average of 32% cost savings after transitioning to our optimized manufacturing and supply chain solutions
Faster Time-to-Market
Our streamlined design and production processes have reduced time-to-market by 22% for medical device clients